Injection Molding Troubleshooting Tips.
Tip #9: Entrapped Air/Blisters
During injection molding, air can become entrapped within the molded part causing a blister to form on the part surface. This often occurs where two flow fronts meet because of variation in part wall thickness or geometry. It can also be caused if air/gas becomes entrapped in the polymer melt which then gets injected into the part during molding.
From a material standpoint blisters can sometimes be caused by wet or improperly dried material. Drying the material correctly will often eliminate blisters if moisture is the cause.
Form a tooling standpoint, blisters can be formed if the mold vents are absent or too small. Insufficient venting does not allow the gases to be effectively removed from the mold during injection of the material.
From a processing standpoint, one of the major causes of blister is insufficient back-pressure on the screw. Back-pressure helps to force any air out the of the resin pellets as they are being compressed in the screw and barrel. If this air is not forced back up through the hopper it becomes entrapped in the melt and gets injected as the part is being filled. Excessive melt temperature and/or residence time can cause the material to degrade and start giving off gaseous degradation products that can cause blisters to form, much like entrapped air does. Reducing melt temperature and/or residence time can help to eliminate potential blisters from forming due to material degradation. Injection speed can also cause blisters to form if the melt front splits due to variation in part geometry or wall thickness variation. Adjusting injection speed up or down will usually reveal if this is the cause of blistering.
While blisters are not a commonly occurring defect, troubleshooting and correcting them is often easily accomplished with a few minor process adjustments.
Entec Polymers Technical Service Team
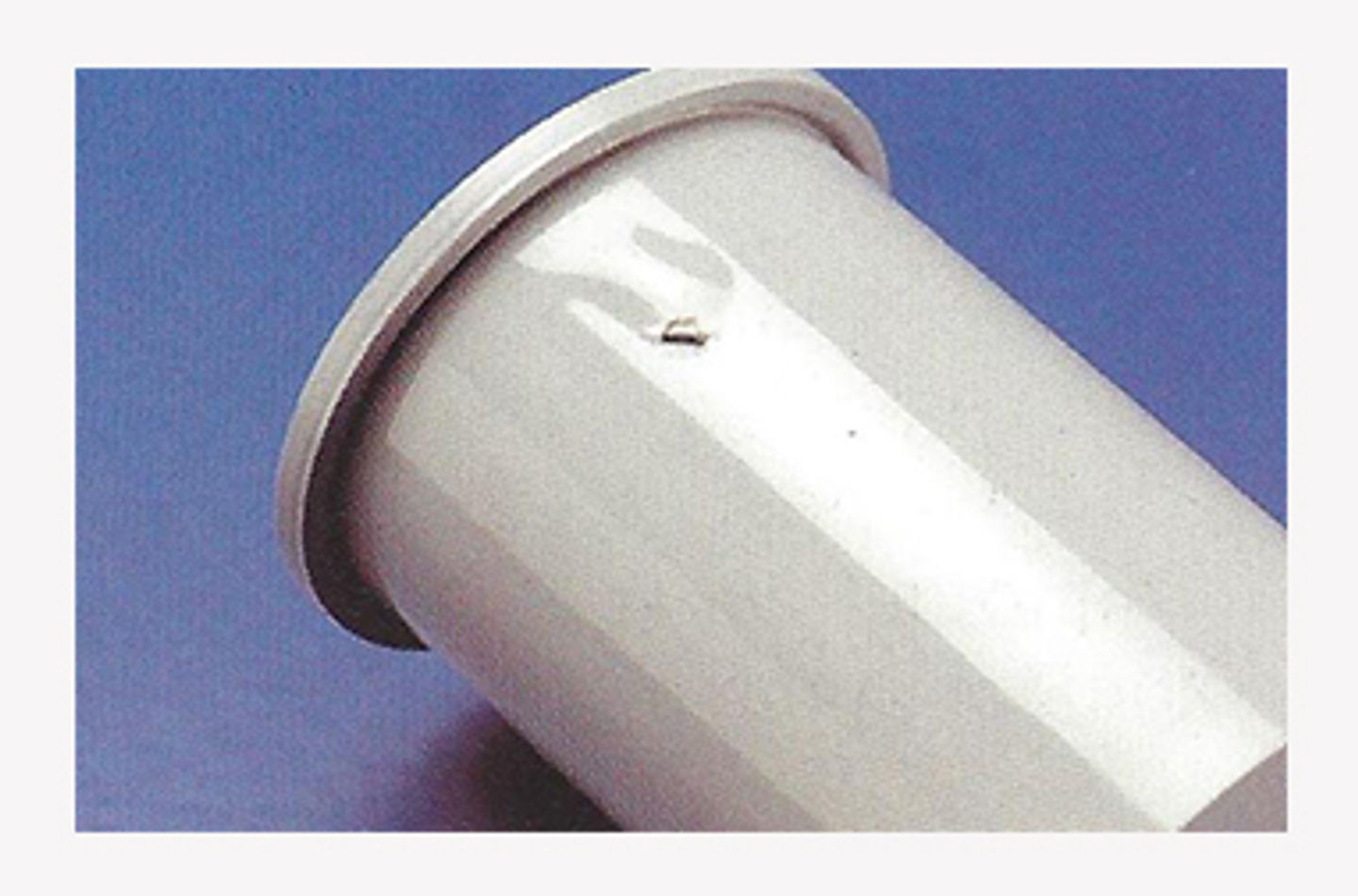